CarbonX PEEK+CF20 Carbon Fiber Reinforced Filament
CarbonX PEEK+CF20 is one of the premier polymers in FFF/FDM 3D Printing. Made using 20% high-modulus chopped carbon fiber for exceptional stiffness, strength, and dimensional stability.
PEEK+CF20 is one of the highest performance thermoplastics ever invented. It is used in some of the most demanding applications by industries such as Auto, Aerospace, Defense, Semi-conductor, and Oil/Gas. Engineers depend on PEEK for applications where failure is not an option.
CarbonX™ PEEK+CF20 Properties Include:
- Superior mechanical properties, even at elevated temperatures
- Excellent chemical resistance
- Low Coefficient of Linear Thermal Expansion (CTE)
- Near Zero moisture absorption
- Low smoke and toxic gas emissions
PEEK+CF20 Thermal Properties:
- Heat Deflection Temperature (HDT) of 320°C
- Glass Transition Temperature (Tg) of 143°C
- Melt Temperature (Tm) of 343°C
- PEEK has an incredible resistance to hydrolysis in boiling water and superheated steam (useful for sterilization and autoclaving) at temperatures in excess of 250°C
Typical PEEK+CF20 Applications Include:
- Seals, Gears, Bushings, Bearings, Pump, and Compressor Components
- Industries served: Auto, Aerospace, Defense, Semi-conductor, Oil & Gas
Printing with CarbonX™ PEEK+CF20
PEEK has a melt temperature (Tm) of 343°C, therefore, you will need an all-metal extruder capable of reaching (and holding) temps upwards of 400°C or more depending on your specific printer. Every printer, slicer, and printing environment is different and you will need to tinker to find a process which works for you. One of the more difficult aspects of printing with PEEK was getting it to stick to the build plate.
Please note: PEEK+CF20 has a tendency to stick to metal (PEEK loves metal). Make sure to purge out your extruder completely before it cools down or you run the risk permanent clogs. Seriously, we know this first hand.
Recommended Print Settings:
- Extruder: 385-415°C
- Bed Temp: 130-150°C
- Nozzle: We currently recommend a hardened steel nozzle with a minimum diameter of 0.4mm.
- Other: Ideal layer height is 60% of nozzle diameter. We do not recommend printing layers smaller than 0.2mm with carbon fiber reinforced filaments.
- Bed Prep: Nano Polymer Adhesive or 3DXTECH Polyimide Tape
- Heated Chamber: Recommended
- Supports: ThermaX™ HTS High-Temp Support was specially designed to work with complex, high-temp materials like this.
- Drying Instructions: 120°C for 4 hours.
Carbon Fiber Reinforced Filament
What Is It? - Fibers 5-10 micrometers wide made of carbon. The fibers are aligned following the axis of the material.This, along with their physical makeup, are what give this material its excellent properties.
What Does It Do? - Carbon Fibers demonstrate a lot of desirable material properties:High stiffness, High tensile strength, High heat tolerance, High chemical resistance, Low weight, &Low thermal expansion
How Does It Work? - Reinforcing plastic with carbon fibers produces a 3D printing filament which exhibits the best properties of both the carbon fibers and the plastic of choice.
What Is It Good For? - Ideal for any applications which require light weight and rigidity. Carbon fiber reinforced parts, designed to use less material and save weight, is extremely popular in aerospace, civil engineering, the military, and motorsports.
Abrasive Material
This material is particularly abrasive among 3D printing filaments. Users may find standard brass nozzles are chewed through very quickly compared to standard wear and tear. When worn through, the nozzle diameter will widen inconsistently and the printer will experience extrusion issues.
Because of this, it's strongly recommended this material be printed through a hardened steel nozzle rather than a softer metal. Hardened steel nozzles can often be inexpensive and easily installed depending on your printer manufacturer's instructions.
3DXTech CarbonX™ PEEK+CF20
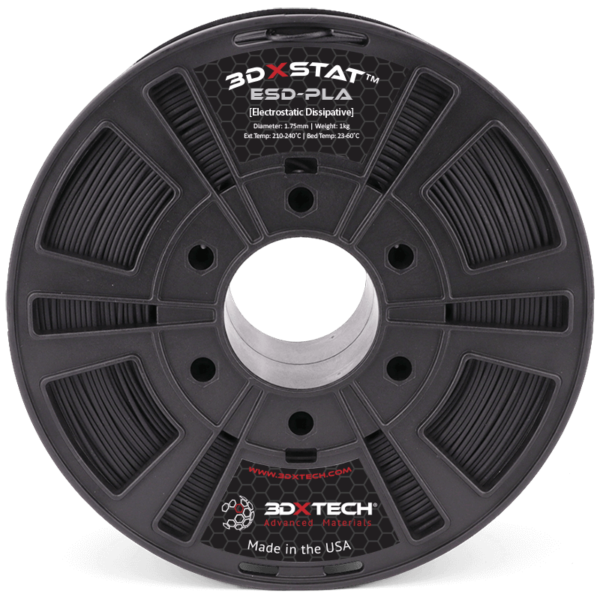
9529 Kč